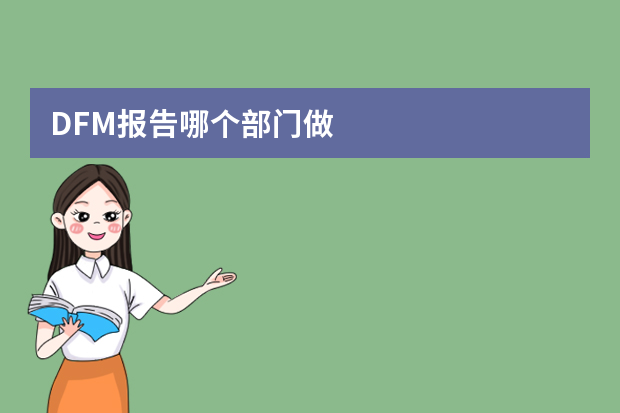
产品开发工程师岗位的工作职责和要求
产品开发工程师岗位的
工作职责
和要求1
职责:
1、跟进现场生产;
2、协调沟通内部生产及销售人员进行产品的需求确认、生产安排、 品质跟踪;
3、进行
数据分析
并制作专业的项目总结报告;
4、对接客户的技术、品质等需求并进行内部沟通;
5、编写作业标准书及进行相关操作培训;
6、严格接受并完成上级交代的其他工作。
任职要求:
1、本科或以上学历;
2、本行业三年及以上工作经验或非本行业的其他制造行业五年及以上工作经验;
3、
沟通能力
出色, 做事细心且有负责心,有学习精神。
产品开发工程师岗位的工作职责和要求2
职责:
1、根据公司各产品需求编制各新产品、新工艺研发项目,研发目的,研发预算,研发周期,并报公司对其可行性和需求进行评估;
2、根据研发项目周期编制研发计划,各节点汇报研发进展,并形成报告;
3、严格按照研发计划制定工作,完成项目的设计、试验、验证,并按时编写并提交相关的技术资料与工作档案;
4、负责研发过程中各部门间的协调工作;
5、负责已完成项目的跟进及维护;
6、不断学习行业内新产品,新技术知识,对技术情报进行检索分析,提供有价值的创意成果;
7、负责项目的进度管理,并定时向公司汇报进展;
8、做好各技术资料、专利等知识成果的部分管理工作
任职要求:
1、本科以上学历,化学,印刷,包装工程,机械等相关专业
2、包装行业相关从业经验3年以上,
马口铁
包装行业2年以上
3、数据分析能力强,勇于创新,自主
管理能力
强
4、较强的协调能力,
抗压能力
强
产品开发工程师岗位的工作职责和要求3
职责:
1、负责新产品项目开发的管理;
2、负责项目产品质量标准与质量目标的制定;
3、负责产品生产过程的
技术支持
;
4、负责生产工艺的培训与考核及实施监督与改进。
任职要求:
1、28—40周岁,大专以上学历,模具或机械相关专业;
2、熟悉模具的设计原理、产品结构的设计与分析,熟悉五金件生产
工艺流程
、行业品质标准;
3、有主导产品结构设计开发五年以上
工作经历
;熟悉五金、塑胶产品的结构设计,熟悉塑胶、压铸成型及
表面处理
工艺;
4、有成功项目开发管理工作经验,统筹能力强;
5、思路清晰,动手能力强,执行力佳。
产品开发工程师岗位的工作职责和要求4
职责:
1、参与产品项目可行性调研,拟制结构、功能设计方案和
项目计划
,研究开发新结构新技术,提升产品性能和质量;
2、参与产品结构、零部件及组装流程的详细设计,BOM/SOP/SPEC相关文件的建立和维护;
3、承担样机的研制、调试和其他相关技术开发;
4、流程分析和DFMA(面向制造和装配的设计)检查;
5、模具、样品、设计更改和零件最终的承认,以及公司所属模具管控;
6、产品开发中的其他问题跟踪以及与技术问题研究;
7、产品量产阶段的必要技术支持。
任职要求:
1、本科或以上学历,
机械设计
、模具或电子类相关专业,或有机械、模具技术专业培训经历;
2、熟悉塑胶/
五金模具
结构及加工工艺,对塑胶/五金及其他常用材料的特性有充分认识,有智能设备、电子电器技术开发经验更佳;
3、有突出的分析和解决问题能力,较强的产品结构、材料分析能力,相关工作经验3年以上;
4、具有产品开发项目管理工作经验,能独立带领开发部门或供应商技术团队完成开发项;。
5、熟练使用Pro/E,CAD等设计软件,能独立完成必要的模具出图、试模、分模等工作;
6、优秀的执行能力、沟通能力、团队管理能力、思维分析能力。
产品开发工程师岗位的.工作职责和要求5
职责:
1、配合业务和客户沟通,能为客户的前期
产品设计
提供现场经验的技术支持。
2、使用Pro/e等3D软件评审客户图档, 制作DFM, 熟练出具合理的2D图面。
3、负责手机金属产品、塑料产品以及压力铸造产品的评估,报价,开模,试产,导入量产整个过程。
4、负责主导工艺及制程开发中的DOE。
5、主导解决项目过程中的问题点。
岗位要求:
1、大专及以上学历,机械设计、模具设计、材料等相关专业。
2、三年及以上手机金属产品、塑料产品以及压力铸造产品的项目开发经验。
3、熟悉手机结构件开发流程,能独立跟进项目从评审到量产全过程,及处理过程中的问题点。
4、熟悉手机结构件冲压成形工艺及模具结构,具有好的品质异常分析能力和解决问题的能力。
5、熟悉手机金属产品、塑料产品以及压力铸造产品等各类产品的前后制程(如冲压、CNC、PVD、电泳、阳极、喷砂、注塑、压铸、焊接等)。
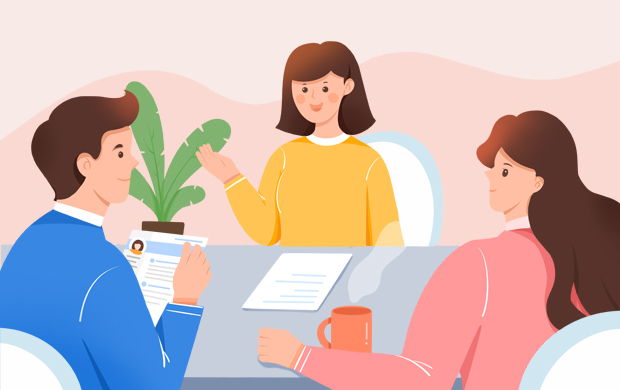
可靠性设计与dfm有何区别?
两者区别:
1、 分析角度不同
DFMEA 分析:DFMEA是设计失效模式及后果分析。设计不合理导致的产品失效, 不考虑制造本身的失效, 只反映设计本身存在问题 ,
PFMEA 分析:PFMEA是对产品生产环节进行分析。制造过程不符合要求导致的产品失效,假设设计是合理
2、 目的不同
DFMEA :识别出关键,重要的产品特性,并制定相关措施保证这些特性达到 。
PFMEA:识别出关键,重要的过程特性, 并制定相关措施保证这些特性符合过程目的。
3、设计过程不同
DFMEA :设计 FMEA ,应用于产品设计时,对产品失效的分析,检查产品设计是否满足所有要求,包括产品功能、性能、法规符合性、顾客特殊要求、可维修性、可用性等要求,有多大的风险,该怎样改进。
PFMEA :过程 FMEA , 应用于产品实现过程设计, 包括原材料采购、 零件生产、 制造、 处理、 成品组装、运输、交付等一些列过程,其中对产品性能以及交付能力影响的因数进行分析, 确认有多大的风险,该怎样改进。
4、失效模式不同
DFMEA 直接对应的产品失效的模式 。
PFMEA 则针对各个环节可能造成产品的失效进行分析 , 两个过程似乎反着进行 。
扩展资料:
DFMEA是一种以预防为主的可靠性设计分析技术,该技术的应用有助于企业提高产品质量,降低成本,缩短研发周期。DFMEA已在航空航天以及国外的汽车行业得到了较为广泛的应用,并显示出了巨大的威力;但在国内汽车行业并没有系统地展开,也没有发挥其应有的作用。
PFMEA是制程失效模式及影响分析(Process Failure Mode and Effects Analysis)的英文简称,是由负责制造/装配的工程师/小组主要采用的一种分析技术,用以最大限度地保证各种潜在的失效模式及其相关的起因/机理已得到充分的考虑和论述。
参考资料:
DFMEA-百度百科
PFMEA-百度百科
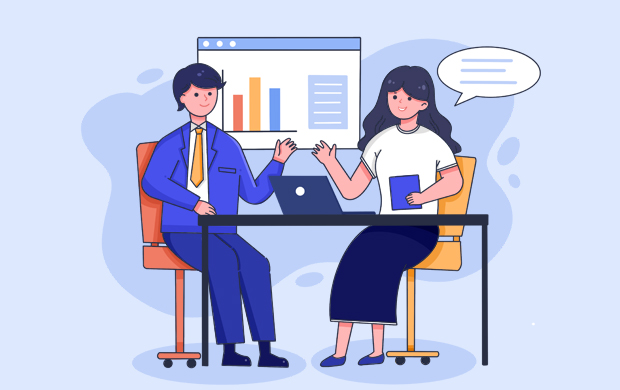
DFM报告哪个部门做
由工程师或设计部门做。
dfm报告指面向制造的设计报告。
当今的DFM是并行工程的核心技术,因为设计与制造是
产品生命周期
中最重要的两个环节,并行工程就是在开始设计时就要考虑产品的可制造性和可装配性等因素。
所以DFM又是并行工程中最重要的支持工具。它的关键是设计信息的工艺性分析、制造合理性评价和改进设计的建议。