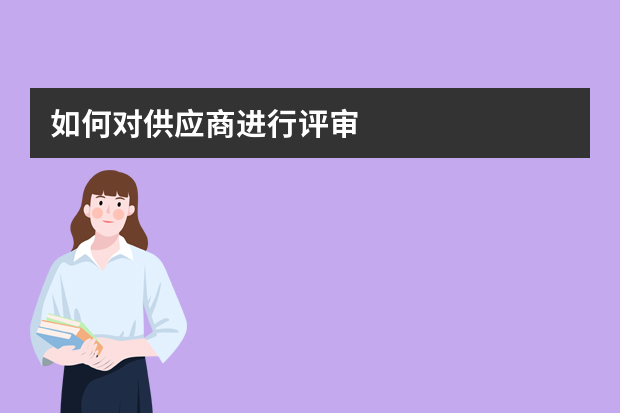
如何对供应商进行评审
1、采购对产品的供应商选定并评价其适合性。
2、供应商评价时按供应商现况调查书及供应商评价表进行评价。增加供应商时作报告书报告。
3、评价分数登录基准。
4、所有供应商评价后80分以上登录,不足80分纠正后可以登录。
5、评价结果适合时登录到厂商目录表中。
6、供应商评价时一般采购可以用相关采购品的产品认证书或成绩书判定。
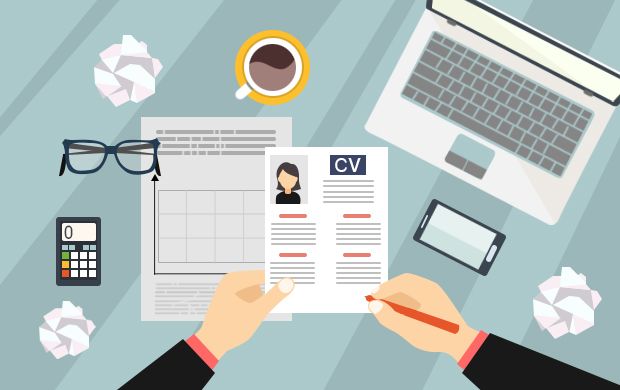
产品质量的8d报告是如何做的?
8d报告八个步骤:
D1-第一步骤:建立解决问题小组——由品质部召集相关人员
若问题无法独立解决,通知你认为有关的人员组成团队。团队的成员必须有能力执行,例如调整机器或懂得改变制程条件,或能指挥作筛选等。
备注:执行者不列入。
D2-第二步骤:描述问题——由品质部收集,并向小组人员传达
向团队说明何时、何地、发生了什么事、严重程度、目前状态、如何紧急处理、以及展示照片和收集到的证物。想象你是FBI的办案人员,将证物、细节描述越清楚,团队解决问题将越快。
D3-第三步骤:执行暂时对策——由小组人员负责执行
若真正原因还未找到,暂时用什么方法可以最快地防止问题?如全检、筛选、将自动改为手动、库存清查等。暂时对策决定后,即立刻交由团队成员带回执行。
备注:为了防止遗漏,纠正措施五要→客户仓库、在途、客户生产线、工厂生产线&工厂仓库。
D4-第四步骤:找出问题真正原因——由小组人员讨论后确定
找问题真正原因时,最好不要盲目地动手改变目前的生产状态,先动动脑。第一件事是要先观察、分析、比较。
列出所知道的所有生产条件(即鱼骨图),逐一观察,看看是否有些条件走样,还是最近有些什么异动?换了夹具吗?换了作业员?换了供应商?换了运输商?修过电源供应器?流程改过?等等不良的发生,总是有原因,资料分析常常可以看出蛛丝马迹。
这样的分析,可以帮助您缩小范围,越来越接近问题核心。当分析完成,列出您认为最有可能的几项,再逐一动手作些调整改变,并且观察哪些改变可使品质回复正常及影响变异的程度,进而找到问题真正的原因。这就是著名田口式方法最简单而实际的运用。
D5-第五步骤:选择永久对策——由小组人员讨论后确定
找到造成问题的主要原因后,即可开始拟出对策的方法。对策的方法也许有好几种,例如修理或更新模具。
试试对可能的选择列出其优缺点,要花多少钱?多少人力?能持续多久?再对可能的方法作一最佳的选择,并且确认这样的对策方法不会产生其它副作用。备注:对策六要→起点改善、模具/工夹具改进、判定标准、辨认标记、隔离处置、产品设计改善。
D6-第六步骤:执行及验证永久对策——由小组人员负责执行并验证
当永久对策准备妥当,则可开始执行及停止暂时对策。并且对永久对策作验证,下游工段及客户己能完全接受,不再产生问题。
D7-第七步骤:防止再发生措施及标准化——由小组人员负责执行
为了防止问题的再发生,要把永久对策落实到设计图纸、工艺文件、检验指导书、模具、工夹具的改进等。
另外对类似的产品,虽然尚未发生问题,亦需作同步改善,防止类似问题在其他产品上再次发生。同时这样的失效,也应列入下一产品研发段的FMEA中予以验证,从源头上彻底防止问题的再发。
D8-第八步骤:团队激励——由运营中心负责确认并负责申报
对于努力解决问题之团队予以嘉勉,使其产生工作上的成就感,并极乐意解决下次碰到的问题。无论是产发段发现的问题,或是量产、客诉问题,若公司每年有近百项的工程问题依照8D的方式来解决,对工程人员实力的培养着实可观,成为公司重要的资产,这也是很多公司将8D制式化的原因。
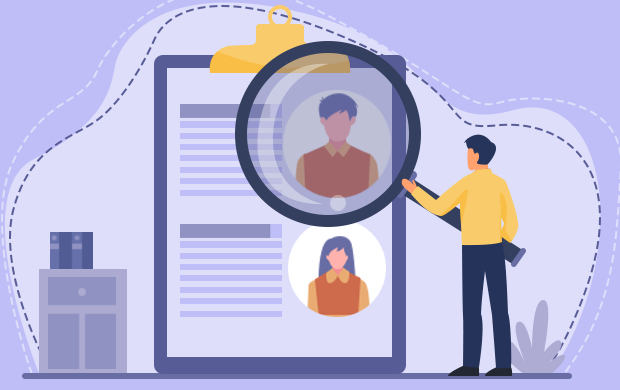
供应商审核报告
一、供应商整体评价
该公司质量管控体系不完善,部分流程缺少标准化,库房摆放混乱,5S管理和目视化管理差,物料无区分。部分工序无作业指导书或没有摆放在员工能看到的地方(没有不良品与合格品的对比图片),员工培训机制不完善。
本次审核通过现场观察和与供方质量人员沟通,我司提出了对供方提高质量管理和质量意识的有效意见,供方极力配合,承诺按我司要求整改,针对专项审核的XXX不良问题,我司按照解决根本原因的标准要求供方购买自动化机器,供方已立项购买设备,所以这次审核已达到预期目的。
二、审核类型:专项审核。
三、审核触发条件
XX月XX日外协厂发现供应商产品AXXX不良问题,该批次的不良率:8.5%,库房的物料全部隔离,没有其他的批次可以使用。五天后供方携带50K物料给我司库房,结果外协厂生产时发现仍有XXX不良的现象。
四、审核目的
通过现场审核找出XXX不良问题的根本原因并提出有效的改进方案,促使避免以后再次出现此问题。根本解决方案为购买自动化机器。
五、具体问题描述
质量管控体系不完善,缺乏质量控制文件及对不合格品的失效分析与改进方案。
产品A生产流程图不规范,没有按照标准方法制作流程图,在流程计划中每个工序无参照标准、责任人、抽样计划、测量计划及测量仪器等。
来料检验库房货物摆放混乱,过道挤满货物,货物摆放过于紧密,无摆放高度限制,货物贴离墙面堆放,物料没有分类,5S管理和目视化管理非常差。
来料检验的抽检工序检验指导书不规范(检验指导书中应包括每个工序的步骤、参考标准、不良与合格的彩色图片对比和规范动作的图片)。
员工培训机制不完善,在全检的工序中员工没有接受正规培训,检验时无操作规范与动作标准。
产品A生产线缺乏自动化设备,无法保证和控制人工失误。建议提交购买计划书与购买设备确切时间。